NEWKer 990TDCa-2 Axis Incremental (Open Loop) Lathe CNC Controller
The NEWKER CNC 990TDCa is a two-axis increment (Open loop) CNC lathe controller known for its economic, stable, and reliable operation. It supports international standard G code, external handheld box operation, and is part of the 990T series by NEWKER. Ideal for Lathe, Turning Center, and various CNC applications.
33%
Product Details
Modbus Technology, ARM, DSP, and FPGA: Modbus is a client/server data communications protocol used for communication between industrial electronic devices. ARM (Advanced RISC Machines) is a microprocessor known for its high performance, low cost, and low power consumption. Digital Signal Processors (DSPs) are microprocessors that process digital signals. Field Programmable Gate Arrays (FPGAs) are semi-custom circuits that can implement any digital device.
-
Vertical CNC Lathe Controller: This controller is designed for vertical CNC lathes, and it supports USB connectivity and control of 2-5 axes.
-
128Mb User Storage: This allows for a large number of programs to be stored on the device.
-
640×480 8 inch Real Colour LCD Display: This provides a clear and vibrant interface for users.
-
Additional Operation Panel and MPG: These provide additional control options for the user.
-
Pulse Output Frequency: The controller supports a pulse output frequency of 5MHz, with a maximum speed of 300m/min and a progressing speed of 0.01-150m/min.
-
USB Movable U Disc Copy Interface and RS232 Interface: These provide additional connectivity options.
-
Spindle Servo Speed Control/Spindle Frequency Conversion Speed Control: This allows for precise control of the spindle speed.
-
Manual Pulse Generator: This provides an additional method for controlling the machine.
-
PLC Programming and Macro Function: The controller supports PLC (Programmable Logic Controller) programming, which is a digital computer used for automation of electromechanical processes. It also supports macro functions, which are sets of instructions that can be used to automate tasks.
-
English Menu, Program, and Interface: The controller’s interface is in English and is designed to be user-friendly.
-
Support for Absolute Encoder Motor and Various Tool Magazines: The controller can work with an absolute encoder motor and supports various types of tool magazines.
-
PLC Function: The PLC function has a refresh cycle of 8ms, and the PLC program can be downloaded via a USB interface and customized.
-
Safety Function: The controller includes several safety features, such as an emergency stop, hardware travel limit, software travel limit, data restoring and recovering, and user-defined alarm hint.
-
General G-code Operation: G-code is a programming language for CNC machines that tells the machine where to move, how fast to move, and what path to follow.
-
Open PLC: The controller supports Open PLC, which is a type of PLC that is not limited to only one programming software.
-
Open Macro Program: The controller supports open macro programs, which are programs that can be edited and customized by the user.
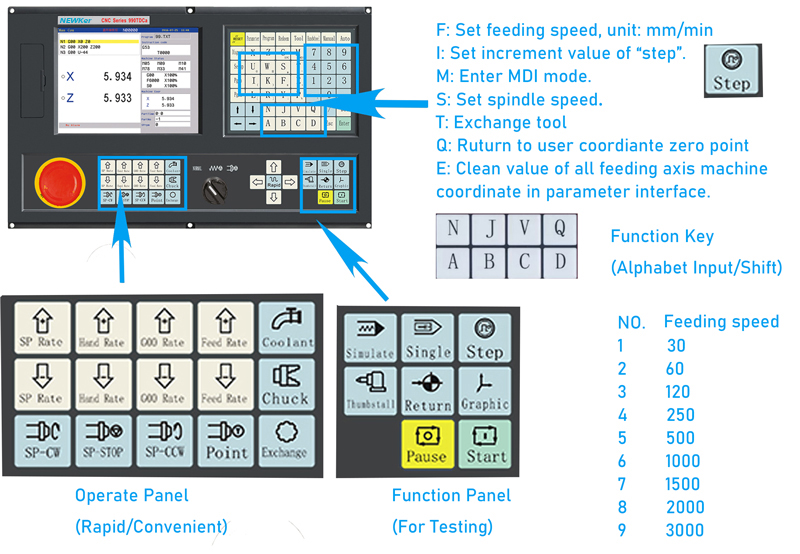
System Function | G code shows | ||
Number of control axis | 3~8(X,Y,Z,A,B,C,Xs,Ys) | Locate rapidly: | G00 |
The smallest programming: | 0.001mm | Straight line interpolation | G01 |
The most programming: | ±99999.999mm | Arc interpolation: | G02/03 |
The highest speed: | 60m/min | Thread cut: | G32 |
Feed speed: | 0.001~30m/min | Cycle of cutting cyliner or cone: | G90 |
Continuous manual: | one axis or multiple axis at the same time | Cycle of cutting end face: | G94 |
Line interpolation: | Straight line, arc, screw thread interpolation | cycle of cutting thread | G92 |
Cutter compensation: | Length of the compansation、radius nose of tool compensation | Fixed cycle of tapping | G93 |
Cutter compensation input: | Try to cut measuring input mode | Cycle of rough cut in excircle | G71 |
Spindle function: | gear、Double analog control、Rigid tapping | Cycle of rough cut at end face: | G72 |
Handwheel function: | panel、handheld | Cycle of closed cut | G73 |
handwheel processing: | The handwheel processing function | Cycle of drill deep hole at end face | G74 |
Screen protection: | The screen protection function | Cycle of cutting groove with external diameter | G75 |
Tool rest function: | Row tool rest、Electric too post 99 knife | Cycle of cutting compound thread | G76 |
Communication function: | RS232、USB interface | Cycle of program | G22,G800 |
Compensation function: | Tool compansation、Space compensation、Screw pitch compensation、Radius compensation | Local coordinate system: | G52 |
Edit program: | Metric/Imperial、Straight thread、taper thread and so on | Detect the instruction of skip | G31,G311 |
Limit position function | soft limit, hard limit | Pole coordinate | G15,G16 |
thread function | metric and inch format, straight thread, taper thread and so on | Metrical/Imperial programme: | G20,G21 |
Preread function: | Preread 10,000 short straight lines | Set coordinate, offset | G184,G185 |
Password protection: | Multilevel password protection | Workpiece coordinate system: | G54~G59 |
Input/output: | I/O 56*24 | Tool radius C | G40,G41,G42 |
PLC programme: | All open PLC design | Accurate locating/continuous path process: | G60/G64 |
Acceleration and deceleration control: | Straight line、Index | Constant linear cutting: | G96/G97 |
Number of encoder: | any setting | Feeding mode: | G98,G99 |
User macro program: | Have | Backing to start point of program: | G26 |
Electrical gear function: | Have | Backing to the fixed point: | G25,G61,G60 |
Subpanel | A type with handwheel; B type with band switch; C type with both A and B, E type | Backing to the datum point: | G28 |
Application: | VMC, grinding, special machine | Suspend: | G04 |
Macro Program: | G65,G66,G67 | ||
Auxiliary function: | S、M、T |